At Mosaic, safety is part of our DNA.
Addressing issues and reducing risk potential means utilizing innovation. This wouldn’t be possible without our dedicated employees who are our front-line eyes and ears for all things safety.
June is National Safety Month. Created in 1996 by the National Safety Council (NSC), the purpose of the month is “to keep each other safe from the workplace to anyplace,” according to the NSC.
This year, the NSC has designated a focus on the topics of safety engagement, roadway safety, risk reduction and slips, trips and falls. Read more about some Mosaic Safety Heroes across these areas who are doing their part to make sure everyone goes home safely each day.
Bartow: Chris Kellum and Philip Thompson
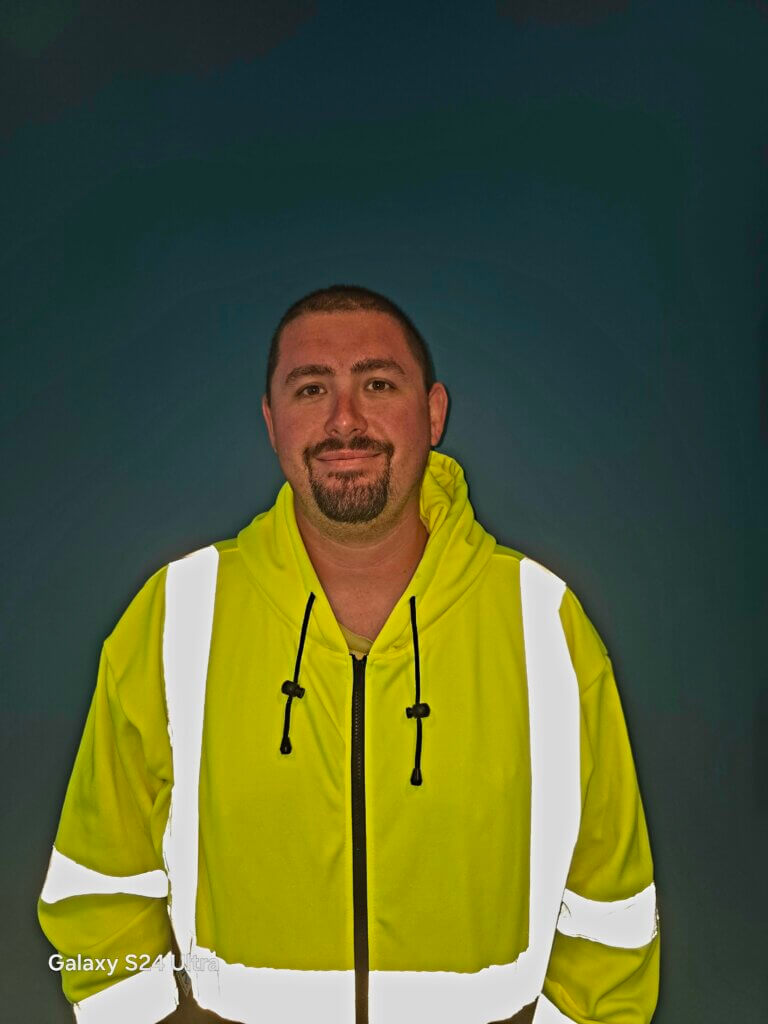
Phosphoric Acid Combo Operator Chris Kellum.
Phosphoric Acid Combo Operator Chris Kellum and Electrical, Instrumentation and Automation (EIA) Philip Thompson are the Safety Heroes at Bartow. Both have had significant impacts on incorporating innovative technology at the site.
Chris is the Area Safety Committee (ASC) Chair. ASCs are employee-led, with front-line employees identifying concerns and potential safety improvements in their area that are then presented to management. Chris piloted using Task Planner in Microsoft Teams for the ASC Rolling Action Item List (RAIL), which allows employees to use standardized documenting initiatives for work orders and Risk Register IDs, as well as assigning actions.
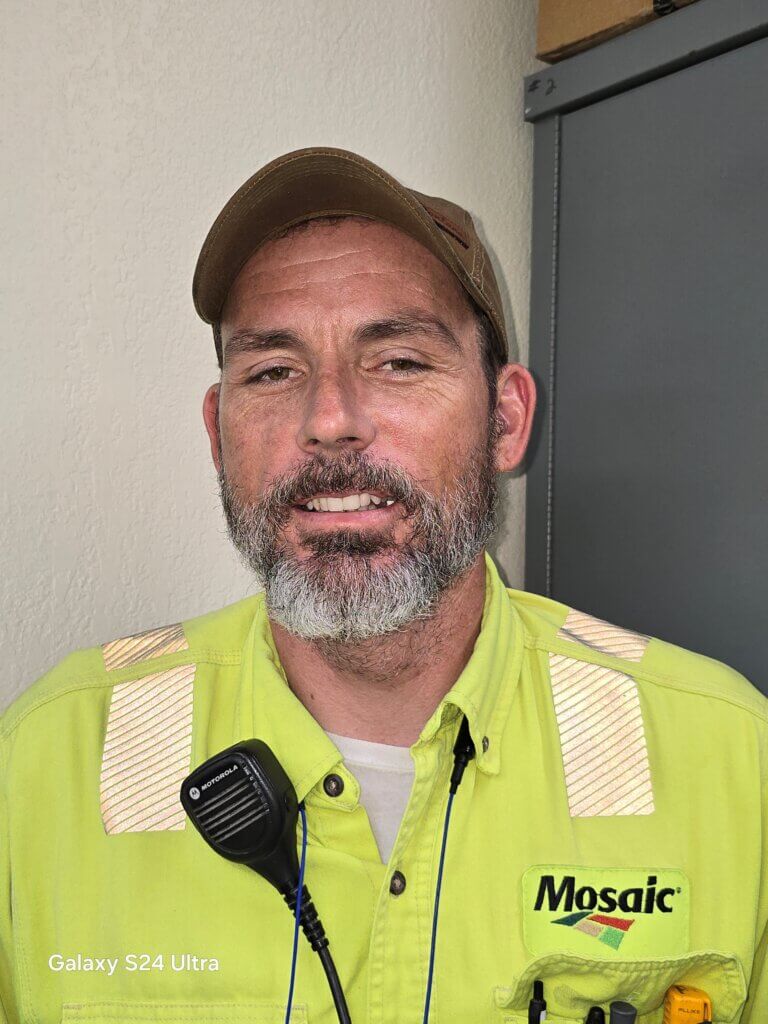
EIA Technician Philip Thompson
“Chris also developed a QR code that allows employees in Phosphoric Acid to scan and report safety concerns, Risk Registers and communicate from front line to the ASC,” said Senior Safety Specialist Jeremy Stalnaker.
Philip is also an ASC. He helped pilot the digital Field Level Hazard Assessment (FLHA) app to use in the department, which helps identify and assess risks before beginning work. Additionally, he took over an ASC with backlogged, inactive items and brought it up to speed. Besides using the Task Planner app, he enters work orders in Maximo and works with the department planner or scheduler to ensure long-term projects don’t lose momentum.
“He does an outstanding job vetting new Risk Register items to ensure they meet criteria and are scored accurately,” Jeremy said. The Risk Register Database is used to document environmental, health and safety risks while documenting operational controls that may mitigate or eliminate the risk.
“Both Chris and Philip do a phenomenal job at organizing these ASC meetings, keeping action items moving through workflow and communicating with management,” Jeremy said.
Four Corners Plant: Art Lamar
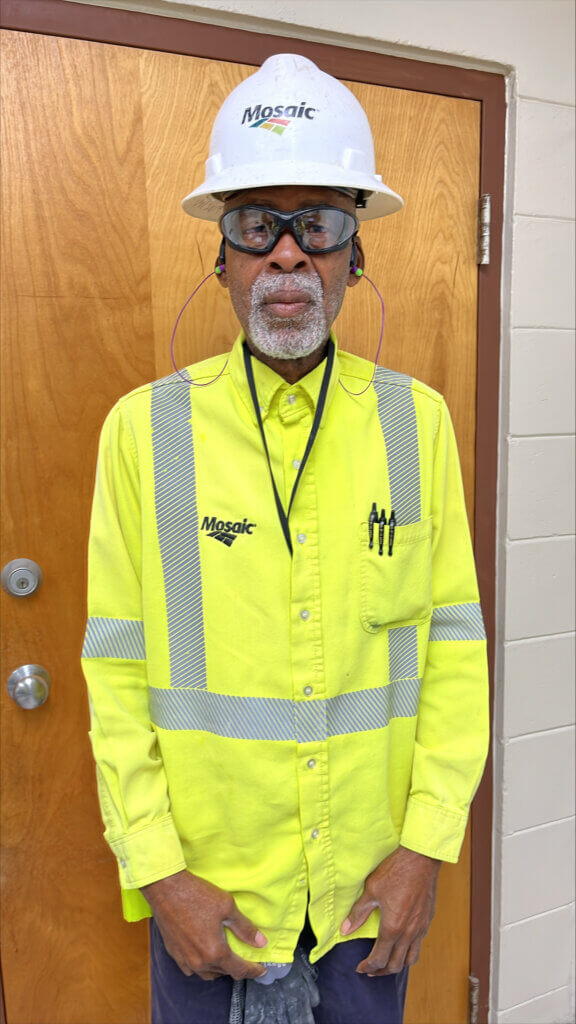
Production Supervisor Art Lamar
Production Supervisor Art Lamar is a 37-year employee. Art transitioned to a shift supervisor more than 20 years ago after working at several different Mosaic and legacy company beneficiation plants. As part of his role, he champions the necessity for proper commitment to safety, housekeeping, identifying and addressing issues, and ensuring all involved parties are fully informed of potential risks and how to mitigate them.
“He is the model of what is wanted from a front-line supervisor,” said Production Superintendent Russell Rosa. “Art’s support of our EHS program is unmatched. Art puts his heart and soul into everything he does, cares about his crew and co-workers, and is an exceptionally hard worker. His commitment to safety is evident through daily face-to-face discussions with all employees, email communication, meetings, shift pass down, and his desire to instill the same safety mindset he has into each and every employee he interacts with, especially new hires. Art truly feels working safe and keeping others safe is his job.”
Four Corners Field: Norma Garcia
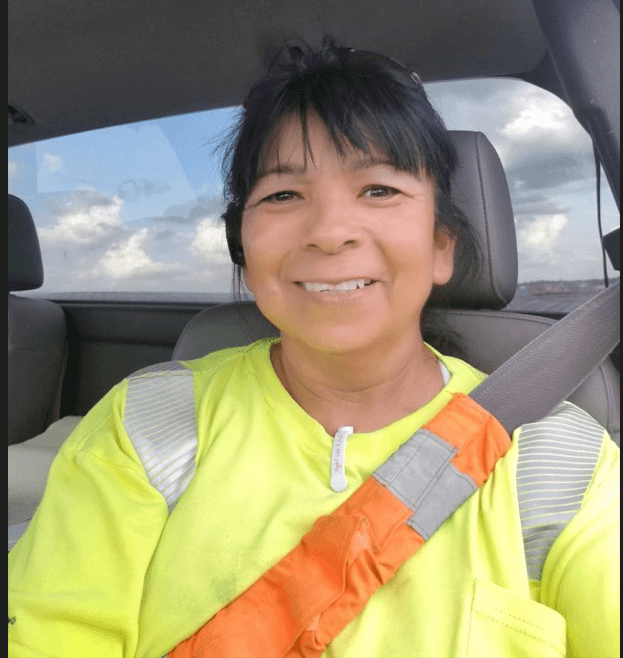
Float Truck Driver Norma Garcia.
Float Truck Driver Norma Garcia has been with Mosaic since 2007. She is an active member of the Safety Committee as well as the Emergency Response Team (ERT). Norma has a strong outlook on safety; going above and beyond to ensure day-to-day tasks like ensuring the accuracy of paperwork, Field Level Hazard Assessments (FLHAs), safe work permits, water permits and more.
“She always identifies any hazards or issues that a lot of people would overlook,” said Area Supervisor William Terrell. “I am grateful to have her on our team!”
New Wales: Terry Carter and Luke LaForce
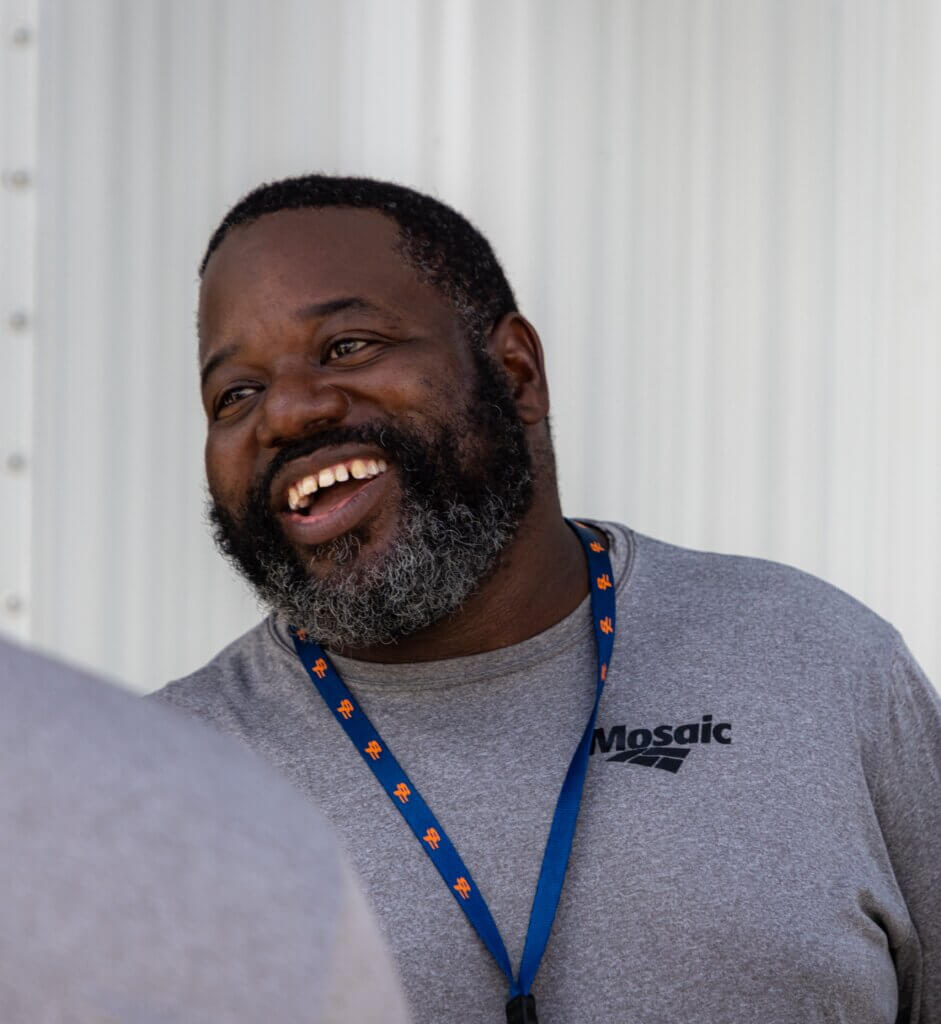
Training Specialist Terry Carter
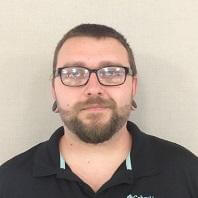
Area Supervisor Luke LaForce.
Training Specialist Terry Carter previously worked as a Safety Coordinator before transitioning to his current role as a training specialist. He is a former ERT captain for the Bartow site, Safety Committee Chairman and Dry Side Area Safety Coordinator. He consolidated ERT training to a single week, improving overall ERT training compliance for the site, and led the ERT at Tallahassee and Sebring competitions. He’s also facilitated emergency response equipment inspections and scheduling, improving long-term use of the equipment. His championship of the ERT and membership encouragement has increased enrollment across the site to ensure emergency response availability of all shifts, weekends and holidays.
“Terry is a super positive employee who is always focused on what’s best for the team,” said General Manager Jody Hilderman. “He’s the perfect candidate for this.”
Area Supervisor Luke LaForce is a daily leader in safety culture and leads by example. Luke has been instrumental in creating training material and qualification standards for safe work between Mosaic and third parties. Additionally, Luke championed the department Management of Change (MOC) process before it was a core part of his daily responsibilities, embracing the process from a safety perspective. The MOC is a set of best practices used when changes are made that could create hazards or disruptions to the business.
In accordance with the training documentation development and leading the way with the MOC process, Luke has also made major contributions to the site Risk Register program by collaborating directly with the safety team to increase focus in relation to safety per project and develop programs to efficiently manage them.
“His attention to small but significant changes in policy helps move the needle on compliance and cultural shift,” said his people leader, Senior Manager, Operations Darren Morrison. “When the most recent Personal Protective Equipment (PPE) change on gloves to always be worn inside the plant took effect, he immediately fitted most everyone in the plant with gloves and gave them access to gloves while explaining the PPE change.
Riverview: Walter Dave Creighton and Nicholas Faratro
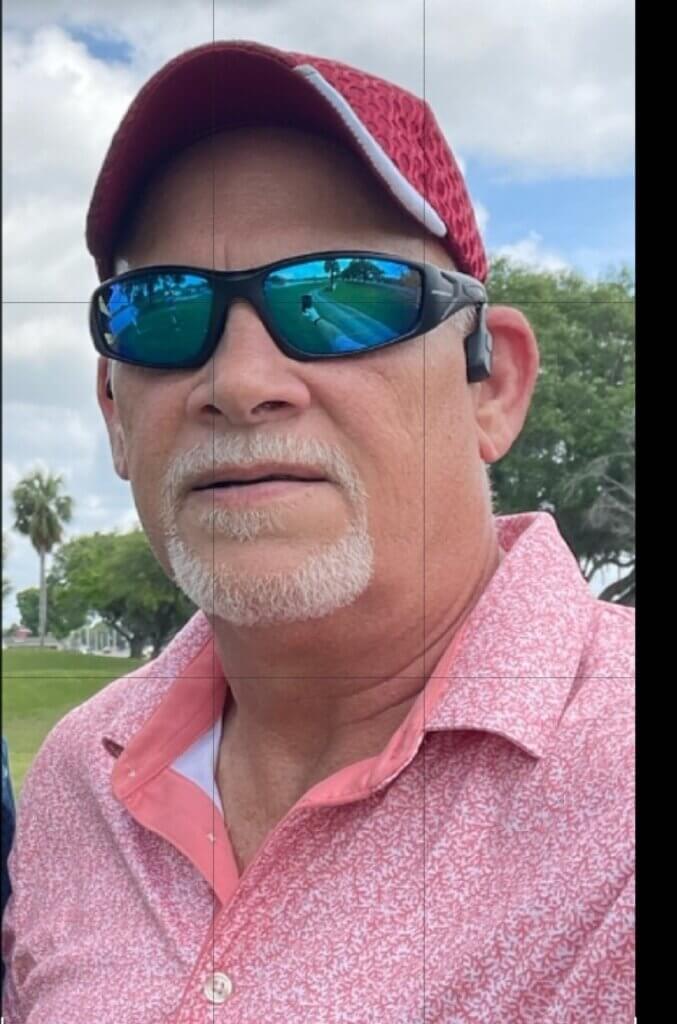
Maintenance Mechanic Walter “Dave” Creighton.
Maintenance Mechanic Walter “Dave” Creighton joined Mosaic in 2010 and has been a member of the ERT since 2013. During his time with the company, he has held various roles and responsibilities including shift supervisor, Risk Register oversight, behavior-based safety permit audits, risk assessments, hazard analysis, dedicated emergency responder and Shift C Incident Commander. His manager, Safety Coordinator Nicholas Faratro, said Dave’s experience is a valuable asset to the Riverview site during emergency events.
“He has a long history as an active participant and supporter in all of his positions,” Nick said. “He demonstrates leadership and professionalism when needed.”
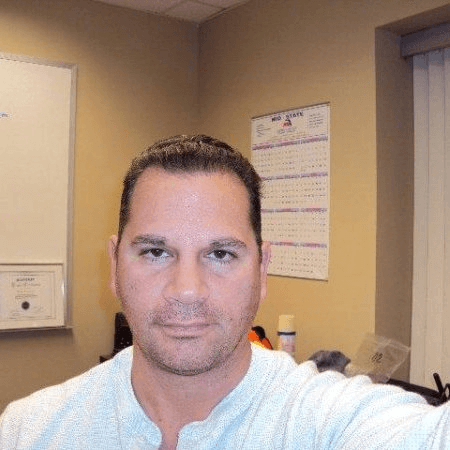
Safety Coordinator Nick Faratro is the leader of the Riverview Emergency Response Team.
Safety Coordinator Nicholas Faratro has served in his role since 2009, providing a tremendous amount of energy and personal commitment. During the recent brush fire at the Riverview facility, Nick served as Incident Commander. This included prioritizing, in order, life safety, incident stabilization and property and environmental preservation. Nick worked tirelessly with site personnel and outside fire and rescue agencies to lead and coordinate response activities so all parties were working toward the same resolution. According to Senior Manager, Health and Safety Todd Smith, Nick is involved in every aspect of safety at the site.
“He is the leader of our site Emergency Response Team, ensuring training and equipment are up to speed and that we are always ready to respond,” said Todd. “His efforts during the recent incident at Riverview were critical to limiting the impacts to our operation. He was also heavily involved in the recovery efforts and the work required to get the facility back online.
South Ft. Meade: Doug Wilson
Shipping and Mobile Equipment Operator Doug Wilson is recognized as a safety hero for his contributions teaching new operators the basics of pushing on the rock piles and how to work safely around drawl holes over tunnels while loading trains. He assists other tractor operators with maintaining loadout piles without being prompted. As a NextGen agent for South Fort Meade, Doug provides constructive feedback for making processes more effective, since NextGen technology focuses on using technology to improve operations and processes. He is also a previous One Mine Employee of the Month.
“His ability to train others, provide effective feedback and take personal ownership of everything he does makes him a Safety Hero,” said Area Supervisor Grant Bonds.
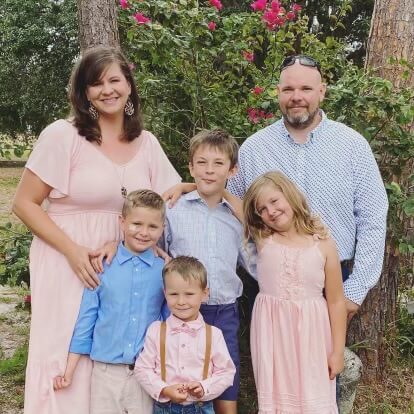
Safety Coordinator Charles “Ryan” Dwyer, far right
Wingate: Charles “Ryan” Dwyer
Safety Coordinator Charles “Ryan” is very passionate about safety and has built up the action-based safety program at both Wingate and Four Corners. In his role, he works with the safety coordinators at South Fort Meade to help them make improvements.
“Ryan is always available to help out his coworkers with any safety concerns or ideas they may have and always follows up with them on solutions,” said Area Coordinator II Brandon Morlan.
Louisiana Operations: Carl “Monkey” Watts
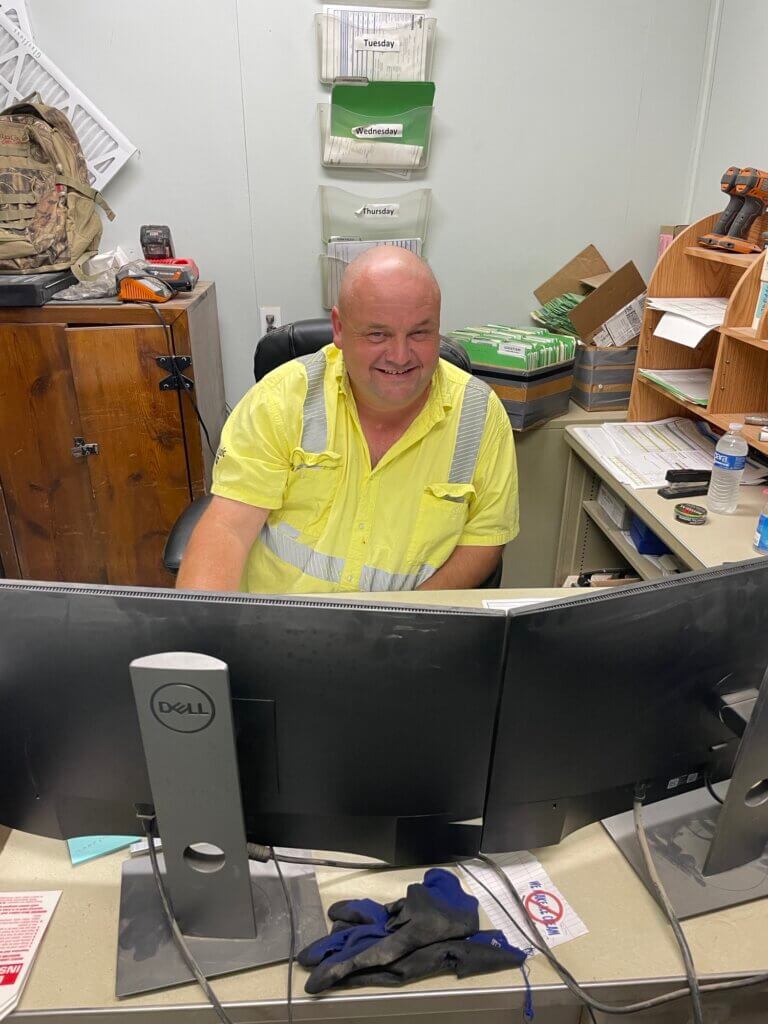
Maintenance Supervisor Carl “Monkey” Watts.
Maintenance Supervisor Carl “Monkey” Watts always incorporates safety in critical decisions when conditions or job plans change. According to Mickey Kraemer, Superintendent, Health and Safety, Carl sets the standard for safety and housekeeping excellence among the crews.
“He addresses the needs or questions of contractors working turnaround quickly, and gets buy-in from management and safety, which instills trust and confidence. During turnaround, he never missed a daily contractor safety meeting and took an active role in them.”
Added Carl, “It’s the work that goes into it as a team that makes sure everyone goes home safe every day.”
Carlsbad: Ron Hatley
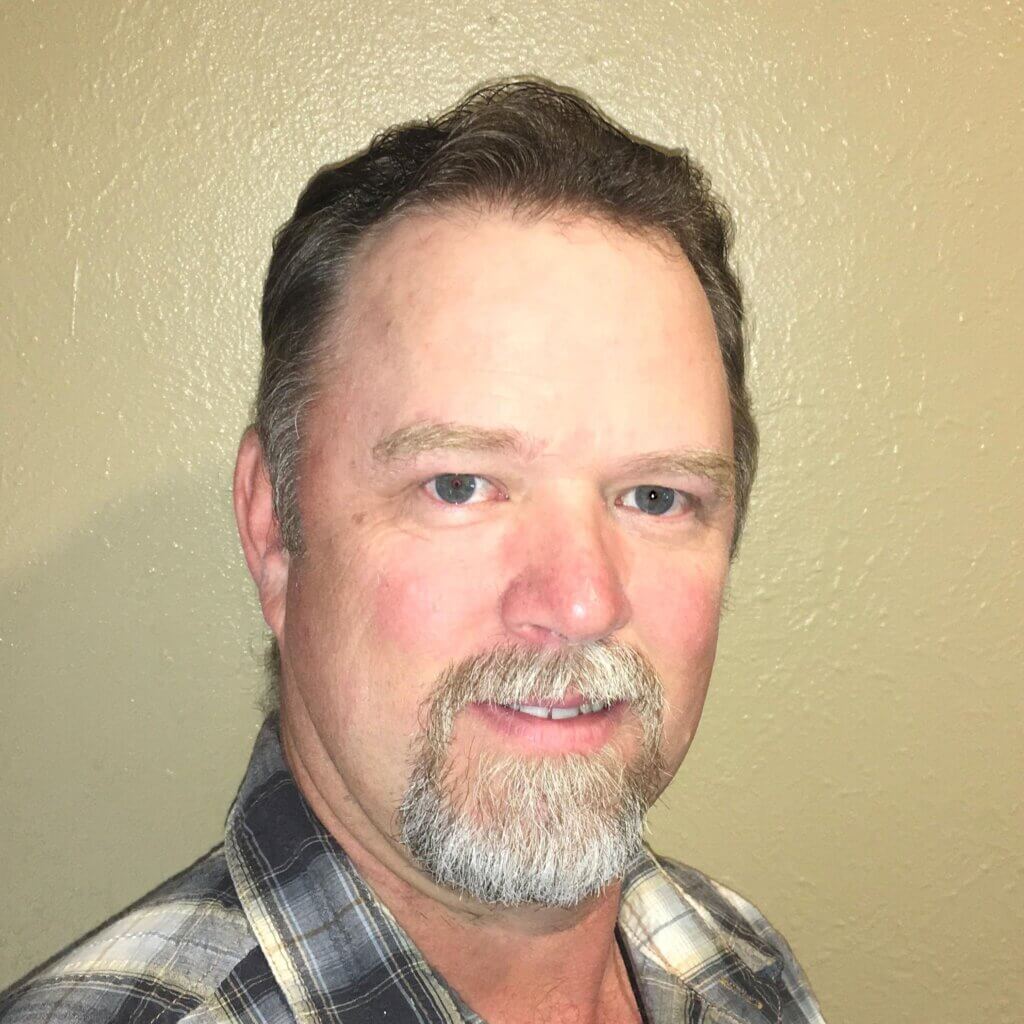
Maintenance Superintendent Ron Hatley.
Maintenance Superintendent Ron Hatley was nominated as the Safety Hero for Carlsbad. Ron proudly embodies the statement, “We don’t do a job unless it can be done safely,” according to Senior Manager, Mine Operations Nicolette Bernardin.
“Last year, Ron led his team to stop jobs with avoidable risk and create thorough, safe work plans,” Nicolette said. “In every conversation with employees, he makes safety personal and seeks to educate.”
Esterhazy: In Memoriam: Vincent Todd Brooks
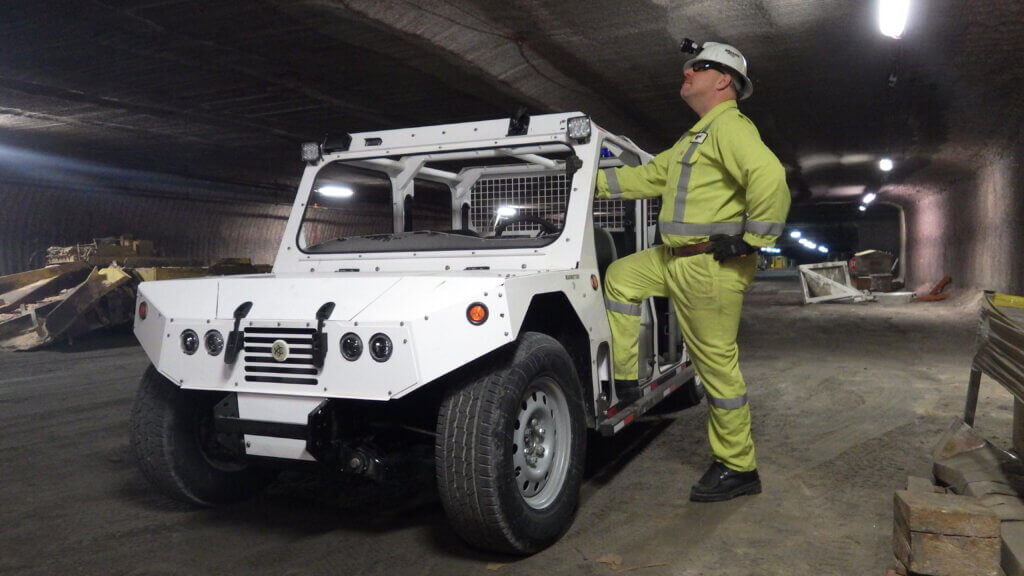
Production Supervisor Vincent “Todd” Brooks.
The final safety hero recognized is Production Supervisor Vincent “Todd” Brooks. Sadly, Todd passed away shortly after this story was published. Our hearts go out to his family, friends and colleagues.
Todd was the co-chair of the Occupational Health Committee (OHC) at K3. He kickstarted the Safe Start Committee at K3 to dig into the specific concerns of those working underground. As an OHC Co-Chair and a Supervisor, he made decisions that were in the best interests of workers and their safety.
“Todd was diplomatic, had a great understanding of our policies and programs, and always had a safety focus in his day-to-day,” said Senior Manager, Health and Safety James Ferstl.
Production Superintendent Scott McMillen added, “Todd took his employees’ concerns seriously. He ensured that he followed up with management and hourly workers and closed the loop to give feedback.”
“He was truly a safety leader and had a positive impact on everyone he worked with,” said Bradley Danylko, Senior Manager, Mine Operations. “Todd was never afraid of change and held numerous roles where he seized every opportunity to drive positive change and make the workplace better for everyone.”